1.7: Glasses
- Page ID
- 408548
\( \newcommand{\vecs}[1]{\overset { \scriptstyle \rightharpoonup} {\mathbf{#1}} } \)
\( \newcommand{\vecd}[1]{\overset{-\!-\!\rightharpoonup}{\vphantom{a}\smash {#1}}} \)
\( \newcommand{\id}{\mathrm{id}}\) \( \newcommand{\Span}{\mathrm{span}}\)
( \newcommand{\kernel}{\mathrm{null}\,}\) \( \newcommand{\range}{\mathrm{range}\,}\)
\( \newcommand{\RealPart}{\mathrm{Re}}\) \( \newcommand{\ImaginaryPart}{\mathrm{Im}}\)
\( \newcommand{\Argument}{\mathrm{Arg}}\) \( \newcommand{\norm}[1]{\| #1 \|}\)
\( \newcommand{\inner}[2]{\langle #1, #2 \rangle}\)
\( \newcommand{\Span}{\mathrm{span}}\)
\( \newcommand{\id}{\mathrm{id}}\)
\( \newcommand{\Span}{\mathrm{span}}\)
\( \newcommand{\kernel}{\mathrm{null}\,}\)
\( \newcommand{\range}{\mathrm{range}\,}\)
\( \newcommand{\RealPart}{\mathrm{Re}}\)
\( \newcommand{\ImaginaryPart}{\mathrm{Im}}\)
\( \newcommand{\Argument}{\mathrm{Arg}}\)
\( \newcommand{\norm}[1]{\| #1 \|}\)
\( \newcommand{\inner}[2]{\langle #1, #2 \rangle}\)
\( \newcommand{\Span}{\mathrm{span}}\) \( \newcommand{\AA}{\unicode[.8,0]{x212B}}\)
\( \newcommand{\vectorA}[1]{\vec{#1}} % arrow\)
\( \newcommand{\vectorAt}[1]{\vec{\text{#1}}} % arrow\)
\( \newcommand{\vectorB}[1]{\overset { \scriptstyle \rightharpoonup} {\mathbf{#1}} } \)
\( \newcommand{\vectorC}[1]{\textbf{#1}} \)
\( \newcommand{\vectorD}[1]{\overrightarrow{#1}} \)
\( \newcommand{\vectorDt}[1]{\overrightarrow{\text{#1}}} \)
\( \newcommand{\vectE}[1]{\overset{-\!-\!\rightharpoonup}{\vphantom{a}\smash{\mathbf {#1}}}} \)
\( \newcommand{\vecs}[1]{\overset { \scriptstyle \rightharpoonup} {\mathbf{#1}} } \)
\( \newcommand{\vecd}[1]{\overset{-\!-\!\rightharpoonup}{\vphantom{a}\smash {#1}}} \)
\(\newcommand{\avec}{\mathbf a}\) \(\newcommand{\bvec}{\mathbf b}\) \(\newcommand{\cvec}{\mathbf c}\) \(\newcommand{\dvec}{\mathbf d}\) \(\newcommand{\dtil}{\widetilde{\mathbf d}}\) \(\newcommand{\evec}{\mathbf e}\) \(\newcommand{\fvec}{\mathbf f}\) \(\newcommand{\nvec}{\mathbf n}\) \(\newcommand{\pvec}{\mathbf p}\) \(\newcommand{\qvec}{\mathbf q}\) \(\newcommand{\svec}{\mathbf s}\) \(\newcommand{\tvec}{\mathbf t}\) \(\newcommand{\uvec}{\mathbf u}\) \(\newcommand{\vvec}{\mathbf v}\) \(\newcommand{\wvec}{\mathbf w}\) \(\newcommand{\xvec}{\mathbf x}\) \(\newcommand{\yvec}{\mathbf y}\) \(\newcommand{\zvec}{\mathbf z}\) \(\newcommand{\rvec}{\mathbf r}\) \(\newcommand{\mvec}{\mathbf m}\) \(\newcommand{\zerovec}{\mathbf 0}\) \(\newcommand{\onevec}{\mathbf 1}\) \(\newcommand{\real}{\mathbb R}\) \(\newcommand{\twovec}[2]{\left[\begin{array}{r}#1 \\ #2 \end{array}\right]}\) \(\newcommand{\ctwovec}[2]{\left[\begin{array}{c}#1 \\ #2 \end{array}\right]}\) \(\newcommand{\threevec}[3]{\left[\begin{array}{r}#1 \\ #2 \\ #3 \end{array}\right]}\) \(\newcommand{\cthreevec}[3]{\left[\begin{array}{c}#1 \\ #2 \\ #3 \end{array}\right]}\) \(\newcommand{\fourvec}[4]{\left[\begin{array}{r}#1 \\ #2 \\ #3 \\ #4 \end{array}\right]}\) \(\newcommand{\cfourvec}[4]{\left[\begin{array}{c}#1 \\ #2 \\ #3 \\ #4 \end{array}\right]}\) \(\newcommand{\fivevec}[5]{\left[\begin{array}{r}#1 \\ #2 \\ #3 \\ #4 \\ #5 \\ \end{array}\right]}\) \(\newcommand{\cfivevec}[5]{\left[\begin{array}{c}#1 \\ #2 \\ #3 \\ #4 \\ #5 \\ \end{array}\right]}\) \(\newcommand{\mattwo}[4]{\left[\begin{array}{rr}#1 \amp #2 \\ #3 \amp #4 \\ \end{array}\right]}\) \(\newcommand{\laspan}[1]{\text{Span}\{#1\}}\) \(\newcommand{\bcal}{\cal B}\) \(\newcommand{\ccal}{\cal C}\) \(\newcommand{\scal}{\cal S}\) \(\newcommand{\wcal}{\cal W}\) \(\newcommand{\ecal}{\cal E}\) \(\newcommand{\coords}[2]{\left\{#1\right\}_{#2}}\) \(\newcommand{\gray}[1]{\color{gray}{#1}}\) \(\newcommand{\lgray}[1]{\color{lightgray}{#1}}\) \(\newcommand{\rank}{\operatorname{rank}}\) \(\newcommand{\row}{\text{Row}}\) \(\newcommand{\col}{\text{Col}}\) \(\renewcommand{\row}{\text{Row}}\) \(\newcommand{\nul}{\text{Nul}}\) \(\newcommand{\var}{\text{Var}}\) \(\newcommand{\corr}{\text{corr}}\) \(\newcommand{\len}[1]{\left|#1\right|}\) \(\newcommand{\bbar}{\overline{\bvec}}\) \(\newcommand{\bhat}{\widehat{\bvec}}\) \(\newcommand{\bperp}{\bvec^\perp}\) \(\newcommand{\xhat}{\widehat{\xvec}}\) \(\newcommand{\vhat}{\widehat{\vvec}}\) \(\newcommand{\uhat}{\widehat{\uvec}}\) \(\newcommand{\what}{\widehat{\wvec}}\) \(\newcommand{\Sighat}{\widehat{\Sigma}}\) \(\newcommand{\lt}{<}\) \(\newcommand{\gt}{>}\) \(\newcommand{\amp}{&}\) \(\definecolor{fillinmathshade}{gray}{0.9}\)INTRODUCTION
When a liquid phase is cooled to below its freezing temperature, it usually transforms into a crystalline solid, i.e. it crystallizes. Some liquids, because of complex molecular configuration or slow molecular transport, do not “crystallize” (assume an ordered configuration) upon being cooled to low temperatures, but instead form a rigid disordered network, known as glass, which is very similar in structure to that of the liquid. Most metals and alkali halides crystallize easily upon cooling through the freezing temperature because the structural rearrangement from the liquid to the crystalline state is simple and bonding is nondirectional. At temperatures just above the freezing temperature, most metals and molten salts have fluidities approximately equivalent to that of water at room temperature. Thus, the required structural rearrangements can take place relatively easily.
In contrast, many inorganic silicates form glasses upon cooling because the fluidity at and even above the freezing temperature is very low. This glass formation is related to the high silicon-oxygen single-bond energies and the directional bonding requirements imposed by \(\mathrm{sp}^3\) hybridization of silicon. The disordered liquid cannot flow easily and thus cannot undergo the rearrangements required for crystallization. Moreover, the fluidity decreases very rapidly as the temperature is lowered. [For large organic and polymeric liquids, crystallization is difficult because of their chain lengths. In polymer systems the intermolecular bonding (Van der Waals) is weak and expected to permit individual molecules to readily slide past one another. Thus, it is the "difficult" structural rearrangement required for crystallization that induces glass formation in these systems.]
The fluidity of liquids (the reciprocal of the viscosity) is a measure of their ability to flow. In turn, the viscosity (\(\eta\)) (fig. 1) is a measure of their resistance to flow.
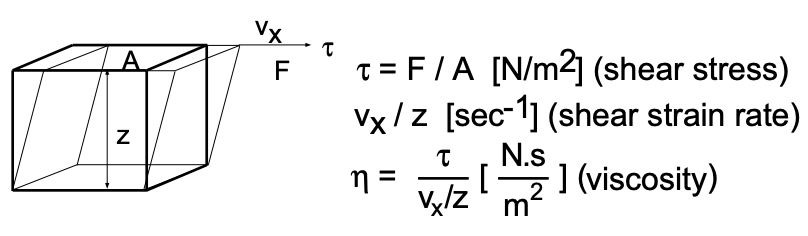
Viscosity is formulated as the ratio of an applied shear stress to the resultant shear-strain rate - its dimensions are Newton seconds per \(\text{meter}^2\). Liquid flow, involving the motion of molecules past one another, requires the breaking and making of new bonds. Thus the fluidity, like chemical reactions and diffusion in solids (to be discussed later) is expected to exhibit an exponential temperature dependence and may be modelled as:
\[\dfrac{1}{\eta} \propto e^{-}\left(\dfrac{\text { Bond Energy }}{k T}\right)\]
It is noteworthy that inorganic glasses occur in nature as do organic glasses (such as the sap from trees) whereas metallic glasses do not occur naturally and have been manufactured only within the last two decades. The major obstacle to achieving metallic glasses was our inability to cool metallic melts to room temperature at rates high enough so that ordering (and thus crystallization) is prevented.
The glass transition point, \(T_g\), (temperature at which a supercooled liquid becomes a glass) is for glasses what the melting point, \(T_m\), is for crystalline solids. Characteristic for almost all glass-forming materials is that at \(T_g\) a change in the temperature dependence of the density \((\Delta \mathrm{V} / \Delta \mathrm{T})\) takes place [where the viscosity is in the range \(10^4\) to \(10^6 \mathrm{Ns} / \mathrm{m}^2\) (the viscosity of \(\mathrm{H}_2 \mathrm{O}\) is \(1.5 \times 10^{-3} \mathrm{Ns} / \mathrm{m}^2\), or about nine orders of magnitude less)]. At higher temperatures (lower viscosities) the structural units are able to reorganize themselves quickly as a quasi-equilibrium liquid. At temperatures below \(T_g\) reorganization among the structural units virtually ceases and the resulting rigid material is referred to as a glass. The experimental value obtained for \(T_g\) depends on the time scale of the experiment. On slow cooling, for example, the structural units have more time to reorganize and, thus, \(T_g\) is lower (fig. 2).
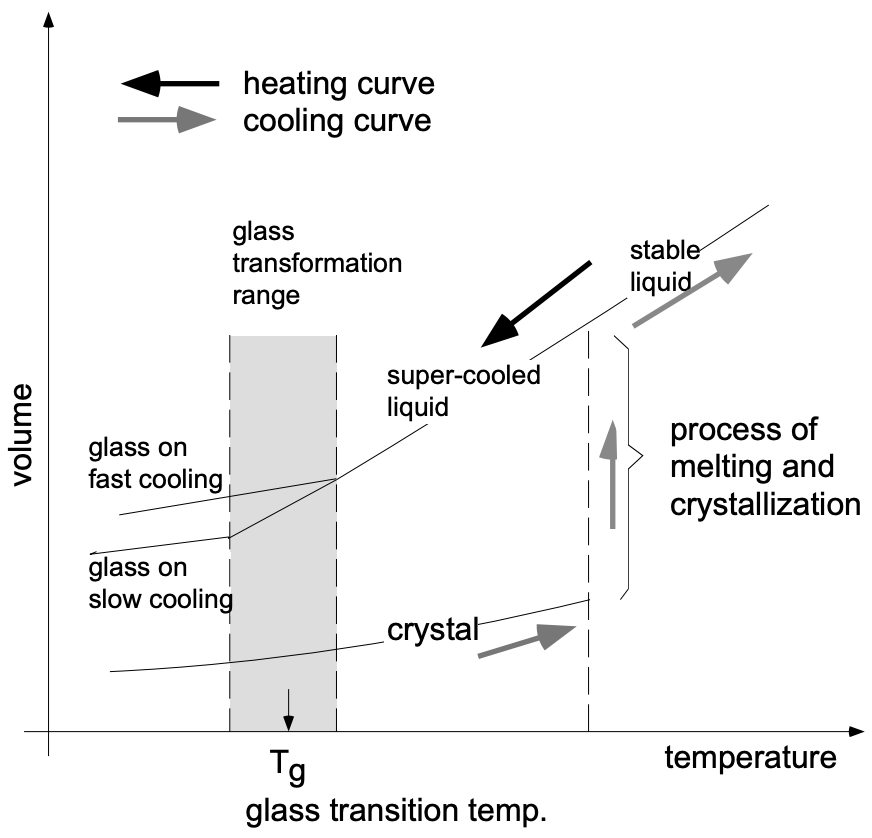
METALLIC GLASSES
The existence of metallic glasses shows the generality of the glass-forming process. In addition, the physical picture in this case is especially simple. Even with the highest presently attainable cooling rates (up to \(10^{7 \circ} \mathrm{C} / \mathrm{s}\) ), no "pure" metal has yet been obtained in a glassy state. However, if the liquid is an alloy of two (or more) metals whose atoms differ greatly in size, the crystallization process is more difficult and can be prevented in many instances by extremely rapid cooling of the melt \(\left(10^{6 \circ} \mathrm{C} / \mathrm{sec}\right)\). The two experimental techniques for rapid cooling are (1) propelling a liquid drop at high velocity and "splatting" it against a cooled copper surface, (2) flattening a liquid drop between a piston and an anvil or between two rolls and (3) "spinning" the melt by transferring it in a continuous mode onto a rapidly rotating, cooled wheel (fig. 3). X-ray patterns of the solidified alloys are similar to those of liquid metals - this and other evidence suggest that they are "amorphous", that their structure is that of a glass.

Another method for preparing metallic glasses is by vacuum deposition onto a substrate cooled to approximately 80K. Again, pure metals crystallize under these conditions, but suitable alloys form glasses, some of which are stable when brought to room temperature. An example is the silver-copper system in which the two solid metals have only about eight percent solubility in each other. If a melt containing 50 wt.\(\%\) silver and 50 wt.\(\%\) copper is slowly cooled, two crystalline phases are produced. When this same alloy is obtained by vacuum deposition, a metastable metallic glass is formed. Initially the glass has metallic electrical conductivity comparable to that of the liquid alloy. When the glass is heated for \(1 / 2\) hour at \(380 \mathrm{~K}\), it converts to a crystalline, metastable face-centered cubic solid solution. Only on heating at about \(500 \mathrm{~K}\) does the equilibrium, two-phase structure form. Many pure nonmetallic elements, however, such as S, Se, Ge and Si, form a stable glass under suitable conditions.
THE GLASSY STATE
The properties and chemical composition of the glass used for optical purposes differ greatly from those of the glass used for baking dishes. Likewise, the glass used for window panes differs from the glass used for artwork or optical purposes. However, (most) inorganic glasses have one thing in common: they are ceramic materials (compounds that contain metallic and non-metallic elements, most often oxygen) with the amorphous structure of a frozen liquid.
Quartz glass is not crystalline at room temperature because the rearrangement of interatomic bonds between \(\mathrm{Si}\) and \(\mathrm{O}\) required for the establishment of order is impeded: the viscosity of glass is so high at room temperature that millions of years would be required for it to crystallize (see above). Hence, glass can be viewed as a perfectly rigid "liquid", being exceptional in that its extraordinarily high viscosity slows down its flow properties even on an expanded time scale.
Upon cooling of liquid “glass” we observe that \(\Delta V/\Delta T\) (the contraction with lowering of T) changes. This may be seen by following the three basic steps in the production of glass: (1) the melting of quartz sand (minute crystals of silica), (2) the shaping of the glass while in a viscous state and (3) the controlled cooling of the shaped article. The \(\mathrm{SiO}_4\) tetrahedra in the sand (crystals) are arranged in an ordered pattern (fig. 4), but in the molten state the crystal matrix breaks up into strings and rings of tetrahedra in irregular patterns (fig. 5). Because the temperature is very high, the groupings continually break up and reform, making the mass fluid.
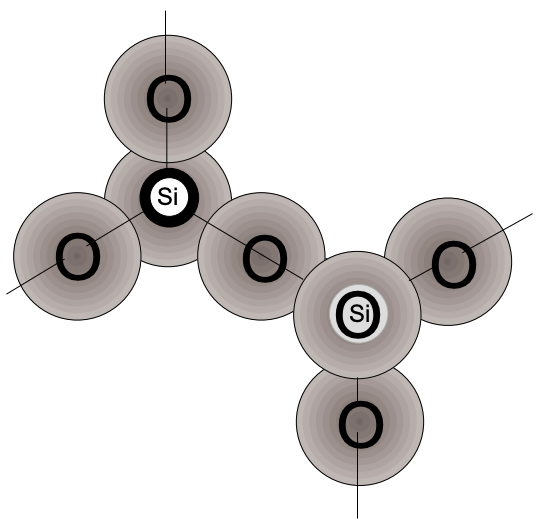
Upon cooling of molten \(\mathrm{SiO}_2\) the tetrahedra form larger groupings and the glass becomes more viscous, permitting it to be shaped by blowing, rolling, pressing, etc. With continuing cooling, larger groupings of tetrahedra form as their kinetic energy decreases. These two phenomena are responsible for the increase in viscosity and the shrinkage that takes place during the cooling period. Beyond the glass transformation temperature changes in configuration of the tetrahedra virtually cease because the glass, to all intents and purposes, has lost its fluidity.
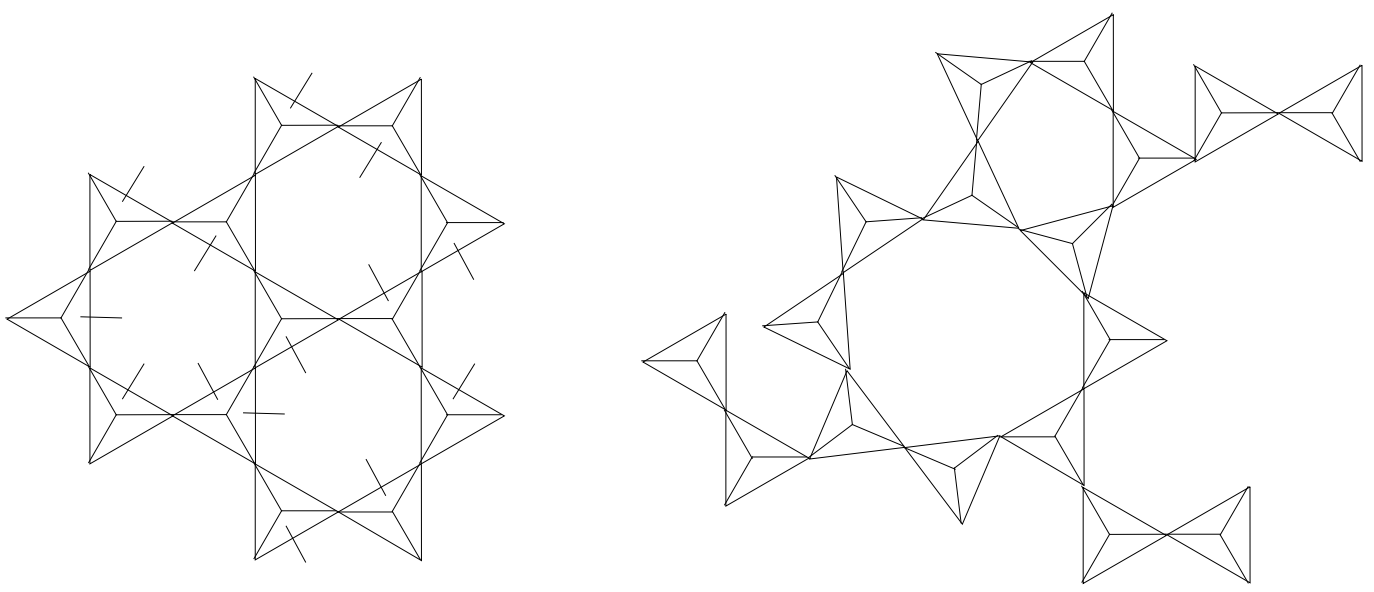
OXIDE GLASSES
The bonding forces responsible for the formation of network structure in crystalline \(\mathrm{SiO}_2\) produce similar networks in glasses of other oxides such as \(\mathrm{B}_2 \mathrm{O}_3\) and \(\mathrm{P}_2 \mathrm{O}_5\) which are thus also considered as primary network formers (the present discussion will be limited to silica glasses). If an oxide, such as \(\mathrm{Na}_2 \mathrm{O}\), is added to silica glass, a bond in the network is broken and the relatively mobile sodium ion becomes a part of the structure (fig. 6). Examples of such network modifiers are \(\mathrm{N}_2 \mathrm{O}, \mathrm{K}_2 \mathrm{O}, \mathrm{Li}_2 \mathrm{O}, \mathrm{CaO}, \mathrm{MgO}\) and \(\mathrm{PbO}\).
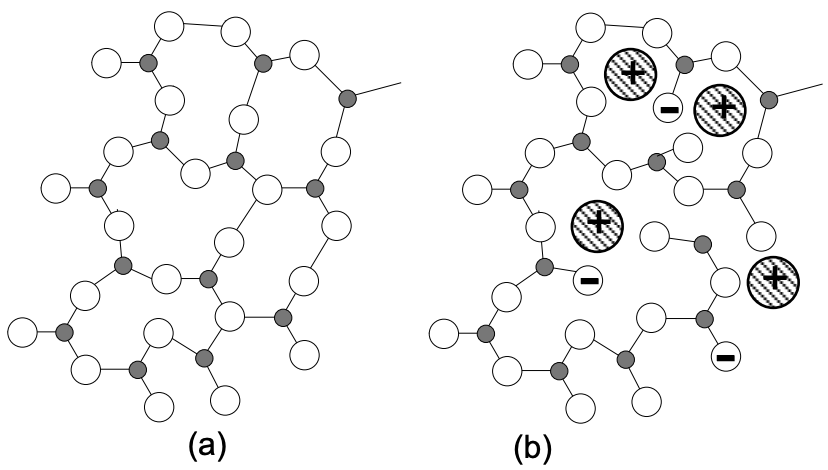
With increase in the amount of modifier, the average number of oxygen-silicon bonds forming bridges between silicon between silicon atoms decreases as follows:
O/Si Ratio in Glass | Bridging-O-Si Bonds/Si atom |
---|---|
2.0 | 4 (fig. 7) |
2.5 | 3 |
3.0 | 2 |
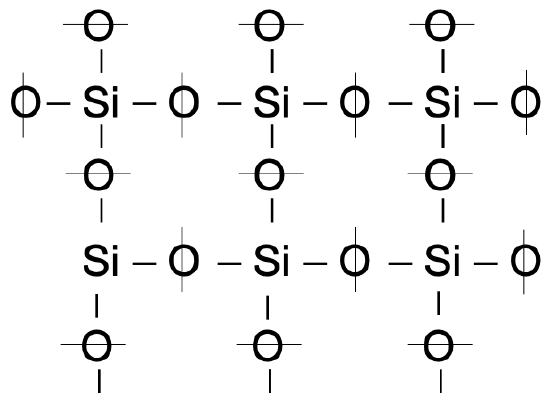
Two bridging bonds per silicon atom will correspond, for example, to a linear chain structure, and any further increase in modifier would reduce the length of the chain. The principal effect of a modifier is to lower the melting and working temperature by decreasing the viscosity. An excess of modifier can make the structural units in the melt sufficiently simple and mobile that crystallization occurs in preference to the formation of a glass.
The compositions and properties of typical glasses are listed in Table 1. Soda-lime glass not only has the advantage of being made from inexpensive raw materials, but also the practical convenience of low working temperatures (fig. 8). Most glass-forming operations (pressing, drawing, etc.) begin at the temperature corresponding to the working point, but can continue while the glass cools.
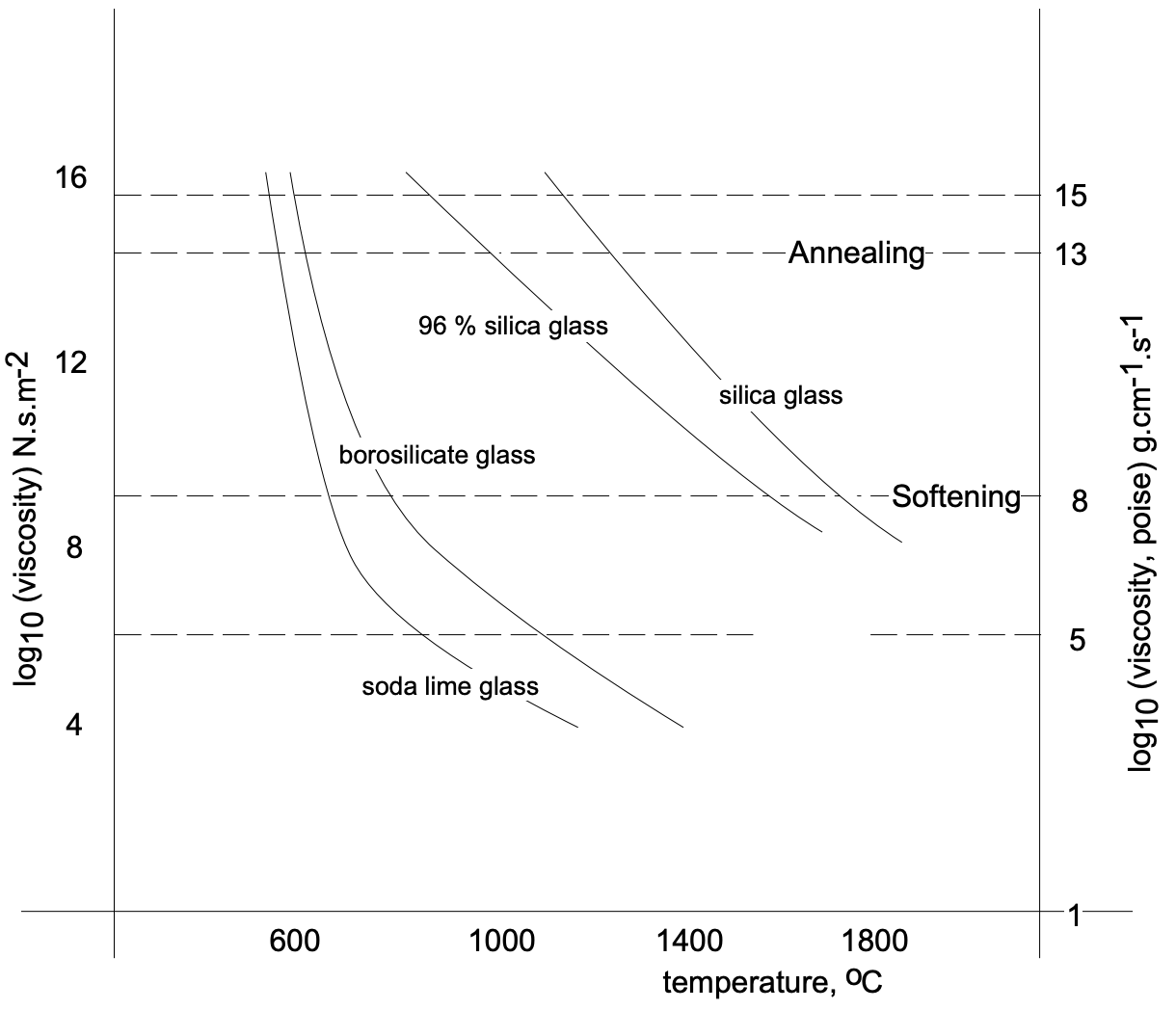
ANNEALING OF GLASS
In order to relieve the internal stresses that may develop during glass formation, all commercial glassware is annealed (slowly cooled) immediately after shaping. This slow cooling operation is carried out in industry by placing the shaped objects on a conveyor belt which transports them first through a reheating zone and then through sections having successively lower temperatures in a furnace called the lehr.
TABLE 1. Typical Oxide Glasses
The transformation of a liquid to a glass actually takes place over a range of temperatures at which the glass shrinks (thermal contraction). The glass does not undergo a change from disordered liquid structure to crystal structure as iron does at its transformation temperature; in glass, the transformation temperature is the temperature below which viscosity prevents any further configurational changes. Any contraction beyond the transformation temperature range is due only to the lower kinetic energy of the groupings.
The transformation temperature of a given “glass composition” depends on its constituents and upon the rate of cooling. Slow cooling results in a lower transformation range because the tetrahedra will have more time to rearrange (to some degree). This results in tighter packing of tetrahedra as the mass reaches its transformation range. When the glass reaches room temperature, its volume will be smaller when cooled slowly than glass melt which has been cooled rapidly. Hence, slower cooling from the melt results in a denser glass. (See fig. 2.)
Glass is thermodynamically unstable at room temperature because configuration changes (which require eons of years to come about!) would result in a lower free energy configuration. However, the changes are so slow that they may be considered negligible.
PROPERTIES OF GLASSES
The strong covalent bonds that exist between the atoms of inorganic glasses plus the lack of crystal structure give glass unusual characteristics. Thus, quartz glass is:
- (a) Chemically stable;
- (b) A poor conductor of heat and electricity;
- (c) Inherently transparent;
- (d) Inherently strong.
Chemical Stability
All glasses are immune to oxidation (decay) because their atoms are fully oxidized. Glass composed of 100 percent silica tetrahedra is extraordinarily inert. It resists the action of most acids (the most notable exception is hydrofluoric acid, utilized to etch glass), but it is attacked by strong alkalis. (The bottles containing liquid alkalis on a chemist’s shelf have a clouded surface.)
Conductivity
The ability of a material to conduct electricity is dependent upon the presence of electrons in the conduction band, separated in glasses by as much as 10eV from the valence band. Because the electrons in glass are tightly bonded, glass is a very poor conductor of electricity - in fact, the large energy gap makes glass an excellent insulator. Glass is also a poor conductor of heat. Thus, hot common glass may crack when cold water is poured onto it because the surface exposed to the cold water will shrink while the dimensions of the interior remain unaffected.
Strength
Glass is harder than many types of steel and is also very elastic, as evidenced by the speed and accuracy with which glass marbles rebound when they meet.
Glass has "no" crystal structure, and hence the phenomenon of slip cannot take place. This, together with the strong bonding between atoms, gives glass a very high compressive strength and a theoretical tensile strength of about \(10^7 \mathrm{kN} / \mathrm{m}^2\) (significantly higher than that of steel). (Glass fibers with an actual tensile strength of \(4 \times 10^7 \mathrm{kN} / \mathrm{m}^2\) have been produced.) Since glass has a "liquid structure" it may be considered "saturated with dislocations". [If a piece of metal has a very high dislocation density (eg., due to cold working) the dislocations interfere with each other's movements. Therefore, with increasing dislocation density a piece of metal becomes harder and stronger, but also more brittle.] Since the molecular structures in glass are unable to move, the presence of minute cracks or imperfections in glass permits stress concentrations to localize and exceed the bond strength between atoms - common glass will crack. Thus, in actual practice, the strength of glass is, by a factor of 100 to 1000, less than the theoretical strength, and glass is brittle. For example, a freshly made electric light bulb may not crack when initially dropped, but its surface becomes damaged and, after it rebounds and strikes the floor a few more times, it breaks.
The inherent high strength of fibrous glass is utilized in the fiberglass sections employed for boats and automobile bodies. Before being pressed into shape fiberglass is mixed with a synthetic resin which serves to protect the fibers from scratching. Since the fibers thus retain their high strength, fiberglass sections are very strong for their weight.
STRENGTHENED GLASS
The glass scientist has produced objects made of glass which can be struck with a hammer or dropped from a tall building without breaking. Two techniques are employed in strengthening glass - one physical and one chemical. Both techniques are based on the fact that, when there is the slightest imperfection (minute scratch) on the surface, glass remains extraordinarily strong in compression but becomes weak in tension. Thus the strengthening treatment consists of prestressing a glass object by inducing compressive strains in its exterior and thereby enabling it to counteract any tensile stresses which develop under tension.
In physical prestressing, the shaped object is heated to just below its softening point (surface flows are annealed out) and its surface is then chilled by means of a blast of air or an oil bath. Under these conditions the exterior of the glass cools and contracts immediately, but since glass is a poor conductor of heat the interior will not contract - the glass will not crack because the interior remains plastic. When the interior starts to cool, it cannot contract because the exterior has already set, but, in attempting to contract, the interior continues to draw the exterior together. A built-in compressive stress then develops in the outer layers of the glass. When a tensile stress is applied to this glass, it is counteracted by these compressive stresses. Thus the prestressed glass will not shatter until the surface compression is exceeded.
As long as its surface remains intact, prestressed glass continues to be strong and shock-resistant. However, if a deep scratch develops on the surface, the tensile stresses set up in the interior by the surface compression are released and the glass will shatter into thousands of tiny particles. Therefore prestressed articles must be cut to exact size and all holes drilled prior to prestressing. Among the many uses for this type of glass are plate-glass doors, side windows of automobiles and portholes of ships.
Ion exchange is a chemical technique for prestressing glass objects. The first step is to place the shaped object into a molten salt bath containing potassium ions, which replace the sodium ions on the surface of the glass. The potassium ions are larger than the sodium ions and, in accommodating them, the surface of the glass becomes more crowded - thus inducing compressive strains on the exterior. Glass of this type, characterized by very high strength, is useful for a great variety of applications. Its flexural strength can be as high as \(10^6 \mathrm{kN} / \mathrm{m}^2\) compared with \(10^5 \mathrm{kN} / \mathrm{m}^2\) for untreated glass.
DEVITRIFICATION OF GLASS
Under certain conditions glass will become “contaminated” with crystalline particles. A glass in this condition is termed devitrified, which is simply another way of stating that it has partially or completely crystallized. Devitrified glass, unless of the very special variety that is deliberately produced, is undesirable since the crystalline areas form large crystals and are extremely weak and brittle, as well as being translucent only. Crystalline segregations in glass are known as stones
RECRYSTALLIZED GLASS (GLASS CERAMICS)
Recrystallized glass, also known as polycrystalline glass, is commonly produced by adding nucleating agents to the glass batch. Subsequently the glass can be formed into a desired shape by any of the conventional glass forming processes and then be heat-treated to promote recrystallization. Recrystallized glass possesses increased impact strength, hardness and thermal shock resistance compared with conventional non-crystalline glasses. One commonplace application of a recrystallized glass is in the manufacture of the so-called refrigerator-to-oven cooking dishes.
COLORED GLASSES
We recognize that glass is normally colorless due to the fact that all electrons are “tightly bonded” and no electronic excitations in the energy range of the visible light spectrum are possible. Glass, however, may be made to absorb selectively in the visible spectrum (thus becoming colored) by any one of three processes:
(1) Addition of ions of transition metals. Such ions provide electronic excitation possibilities to visible light. Typical ions added are:
\begin{aligned}
&\mathrm{Cr}^{++} \quad &&\text{blue} \\
&\mathrm{Cr}^{+++} \quad &&\text{green} \\
&\mathrm{Co}^{++} \quad &&\text{pink} \\
&\mathrm{Mn}^{++} \quad &&\text{orange} \\
&\mathrm{Fe}^{++} \quad &&\text{blue-green}
\end{aligned}
(2) Addition of colloidal particles ( \(\phi\) \(40\) to \(2000 \AA\) ). These small particles, while not impeding light transmission (because of their small size) exhibit selective absorption and complementary reflection. Au particles (at \(10^{-4} \mathrm{~g} / \mathrm{cm}^3\) ) give colors which vary with particle size:
\begin{aligned}
&\mathrm{Au} \quad &&\phi 4-10 \mathrm{~nm} \quad &\text{pink} \\
&\mathrm{Au} \quad &&\phi 10-75 \mathrm{~nm} \quad &\text{ruby} \\
&\mathrm{Au} \quad &&\phi 75-110 \mathrm{~nm}\quad &\text{green} \\
&\mathrm{Au} \quad &&\phi 110-170 \mathrm{~nm} \quad &\text{brown}
\end{aligned}
(3) Addition of colored crystals. Some glasses are colored by means of crystals dispersed throughout. An example is the scarlet glass made by the early Egyptians (brought about by the addition of red copper oxide). Another example is red color from the addition of red \(\mathrm{Pb}_2 \mathrm{CrO}_6\) whereas \(\mathrm{Cr}_2 \mathrm{O}_3\) yields green color.
GLASS FIBER
Glass fiber, or fiberglass* as it is commonly known, is glass in fiber form. It is made by one of several processes, each of which involves the drawing out of the filaments from glass in the viscous state. Modern technical developments date from World War I when Germany had to find a substitute for asbestos as insulating material.
The process whereby continuous filament glass fiber is made is particularly interesting. The glass batch is melted in the glass tank furnace and the molten glass is molded into ordinary sized marbles. These marbles are fed into an electric furnace which has a platinum-alloy bushing containing many tiny holes. When the glass marbles reach the holes, the glass flows through them and is drawn down vertically, forming individual filaments. These filaments can then be twisted into a “yarn” and spun on normal textile spindles as required. About one third of an ounce of glass produces about one hundred miles of filament at a rate of about 6,000 feet per minute.
Glass wool, on the other hand, is produced by a different process. The most common technique, known as the Crown process, produces a thick matte of short glass fibers which are held together by a polymer binder. In the Crown method, a thick stream of molten glass is poured into a rapidly rotating steel dish that has tiny vents around its periphery. The glass is forced through these vents by centrifugal force, forming relatively short fibers with diameters of about 0.0007 cm. The matte is then passed through curing ovens where the binder sets and is then cut into sizes suitable for insulation.
- *
-
Fiberglass is really a registered trade name.
SHEET AND PLATE GLASS PRODUCTION
The main types of flat glass produced are drawn sheet and float glass. The processes involved are highly automated.
Flat drawn glass is used for windows and other applications where accuracy of thickness and a high surface finish are not vital. In this process the molten glass is drawn up vertically from the end of a large rectangular tank furnace, the thickness of the drawn sheet being controlled principally by the size of the slot in the steel form held just above the surface of the molten glass. A steel starting dummy is used to commence the drawing action, but this is cracked off once it passes through. Once started, this process is continuous, the cooled and solidified sheet merely being cracked off in suitable lengths once it leaves the rolls.
The float process is the most recent advance in the production of plate glass with a high surface finish. In the float process, flat, fire-finished, stress-free glass is formed by preventing contact between the glass sheet and anything solid. The glass leaves the glass-tank in a continuous molten strip and is floated immediately onto the surface of a bath of molten tin. The tin bath is surrounded by a non-oxidizing atmosphere and, while in this atmosphere, the glass is heated sufficiently to prevent the development of internal stresses. As the glass sheet leaves the float bath chamber it enters an annealing furnace. Glass produced by the float process is free from distortion and has fire-finished surfaces that are smoother and flatter than those of normal polished plate glass.