23.2: Principles of Extractive Metallurgy
- Page ID
- 24342
\( \newcommand{\vecs}[1]{\overset { \scriptstyle \rightharpoonup} {\mathbf{#1}} } \)
\( \newcommand{\vecd}[1]{\overset{-\!-\!\rightharpoonup}{\vphantom{a}\smash {#1}}} \)
\( \newcommand{\id}{\mathrm{id}}\) \( \newcommand{\Span}{\mathrm{span}}\)
( \newcommand{\kernel}{\mathrm{null}\,}\) \( \newcommand{\range}{\mathrm{range}\,}\)
\( \newcommand{\RealPart}{\mathrm{Re}}\) \( \newcommand{\ImaginaryPart}{\mathrm{Im}}\)
\( \newcommand{\Argument}{\mathrm{Arg}}\) \( \newcommand{\norm}[1]{\| #1 \|}\)
\( \newcommand{\inner}[2]{\langle #1, #2 \rangle}\)
\( \newcommand{\Span}{\mathrm{span}}\)
\( \newcommand{\id}{\mathrm{id}}\)
\( \newcommand{\Span}{\mathrm{span}}\)
\( \newcommand{\kernel}{\mathrm{null}\,}\)
\( \newcommand{\range}{\mathrm{range}\,}\)
\( \newcommand{\RealPart}{\mathrm{Re}}\)
\( \newcommand{\ImaginaryPart}{\mathrm{Im}}\)
\( \newcommand{\Argument}{\mathrm{Arg}}\)
\( \newcommand{\norm}[1]{\| #1 \|}\)
\( \newcommand{\inner}[2]{\langle #1, #2 \rangle}\)
\( \newcommand{\Span}{\mathrm{span}}\) \( \newcommand{\AA}{\unicode[.8,0]{x212B}}\)
\( \newcommand{\vectorA}[1]{\vec{#1}} % arrow\)
\( \newcommand{\vectorAt}[1]{\vec{\text{#1}}} % arrow\)
\( \newcommand{\vectorB}[1]{\overset { \scriptstyle \rightharpoonup} {\mathbf{#1}} } \)
\( \newcommand{\vectorC}[1]{\textbf{#1}} \)
\( \newcommand{\vectorD}[1]{\overrightarrow{#1}} \)
\( \newcommand{\vectorDt}[1]{\overrightarrow{\text{#1}}} \)
\( \newcommand{\vectE}[1]{\overset{-\!-\!\rightharpoonup}{\vphantom{a}\smash{\mathbf {#1}}}} \)
\( \newcommand{\vecs}[1]{\overset { \scriptstyle \rightharpoonup} {\mathbf{#1}} } \)
\( \newcommand{\vecd}[1]{\overset{-\!-\!\rightharpoonup}{\vphantom{a}\smash {#1}}} \)
\(\newcommand{\avec}{\mathbf a}\) \(\newcommand{\bvec}{\mathbf b}\) \(\newcommand{\cvec}{\mathbf c}\) \(\newcommand{\dvec}{\mathbf d}\) \(\newcommand{\dtil}{\widetilde{\mathbf d}}\) \(\newcommand{\evec}{\mathbf e}\) \(\newcommand{\fvec}{\mathbf f}\) \(\newcommand{\nvec}{\mathbf n}\) \(\newcommand{\pvec}{\mathbf p}\) \(\newcommand{\qvec}{\mathbf q}\) \(\newcommand{\svec}{\mathbf s}\) \(\newcommand{\tvec}{\mathbf t}\) \(\newcommand{\uvec}{\mathbf u}\) \(\newcommand{\vvec}{\mathbf v}\) \(\newcommand{\wvec}{\mathbf w}\) \(\newcommand{\xvec}{\mathbf x}\) \(\newcommand{\yvec}{\mathbf y}\) \(\newcommand{\zvec}{\mathbf z}\) \(\newcommand{\rvec}{\mathbf r}\) \(\newcommand{\mvec}{\mathbf m}\) \(\newcommand{\zerovec}{\mathbf 0}\) \(\newcommand{\onevec}{\mathbf 1}\) \(\newcommand{\real}{\mathbb R}\) \(\newcommand{\twovec}[2]{\left[\begin{array}{r}#1 \\ #2 \end{array}\right]}\) \(\newcommand{\ctwovec}[2]{\left[\begin{array}{c}#1 \\ #2 \end{array}\right]}\) \(\newcommand{\threevec}[3]{\left[\begin{array}{r}#1 \\ #2 \\ #3 \end{array}\right]}\) \(\newcommand{\cthreevec}[3]{\left[\begin{array}{c}#1 \\ #2 \\ #3 \end{array}\right]}\) \(\newcommand{\fourvec}[4]{\left[\begin{array}{r}#1 \\ #2 \\ #3 \\ #4 \end{array}\right]}\) \(\newcommand{\cfourvec}[4]{\left[\begin{array}{c}#1 \\ #2 \\ #3 \\ #4 \end{array}\right]}\) \(\newcommand{\fivevec}[5]{\left[\begin{array}{r}#1 \\ #2 \\ #3 \\ #4 \\ #5 \\ \end{array}\right]}\) \(\newcommand{\cfivevec}[5]{\left[\begin{array}{c}#1 \\ #2 \\ #3 \\ #4 \\ #5 \\ \end{array}\right]}\) \(\newcommand{\mattwo}[4]{\left[\begin{array}{rr}#1 \amp #2 \\ #3 \amp #4 \\ \end{array}\right]}\) \(\newcommand{\laspan}[1]{\text{Span}\{#1\}}\) \(\newcommand{\bcal}{\cal B}\) \(\newcommand{\ccal}{\cal C}\) \(\newcommand{\scal}{\cal S}\) \(\newcommand{\wcal}{\cal W}\) \(\newcommand{\ecal}{\cal E}\) \(\newcommand{\coords}[2]{\left\{#1\right\}_{#2}}\) \(\newcommand{\gray}[1]{\color{gray}{#1}}\) \(\newcommand{\lgray}[1]{\color{lightgray}{#1}}\) \(\newcommand{\rank}{\operatorname{rank}}\) \(\newcommand{\row}{\text{Row}}\) \(\newcommand{\col}{\text{Col}}\) \(\renewcommand{\row}{\text{Row}}\) \(\newcommand{\nul}{\text{Nul}}\) \(\newcommand{\var}{\text{Var}}\) \(\newcommand{\corr}{\text{corr}}\) \(\newcommand{\len}[1]{\left|#1\right|}\) \(\newcommand{\bbar}{\overline{\bvec}}\) \(\newcommand{\bhat}{\widehat{\bvec}}\) \(\newcommand{\bperp}{\bvec^\perp}\) \(\newcommand{\xhat}{\widehat{\xvec}}\) \(\newcommand{\vhat}{\widehat{\vvec}}\) \(\newcommand{\uhat}{\widehat{\uvec}}\) \(\newcommand{\what}{\widehat{\wvec}}\) \(\newcommand{\Sighat}{\widehat{\Sigma}}\) \(\newcommand{\lt}{<}\) \(\newcommand{\gt}{>}\) \(\newcommand{\amp}{&}\) \(\definecolor{fillinmathshade}{gray}{0.9}\)- Discuss how coordination chemistry can be applied in metallurgic processes.
- Understanding the thermodynamics of Pyrometallurgy
The Earth formed from the same cloud of matter that formed the Sun, but the planets acquired different compositions during the formation and evolution of the solar system. In turn, the natural history of the Earth caused parts of this planet to have differing concentrations of the elements. The mass of the Earth is approximately 5.98×1024 kg. In bulk, by mass, it is composed mostly of iron (32.1%), oxygen (30.1%), silicon (15.1%), magnesium (13.9%), sulfur (2.9%), nickel (1.8%), calcium (1.5%), and aluminum (1.4%); with the remaining 1.2% consisting of trace amounts of other elements. Figure \(\PageIndex{1}\) illustrates the relative atomic-abundance of the chemical elements in Earth's upper continental crust, which is relatively accessible for measurements and estimation.
Many of the elements shown in the graph are classified into (partially overlapping) categories:
- rock-forming elements (major elements in green field, and minor elements in light green field);
- rare earth elements (lanthanides, La-Lu, and Y; labeled in blue);
- major industrial metals (global production >~3×107 kg/year; labeled in red);
- precious metals (labeled in purple);
- the nine rarest "metals" (the six platinum group elements and Au, Re, and Te) are in the yellow field.
Most metals are found as types of rock in the Earth's crust. These ores contain sufficient minerals with important elements including metals that can be economically extracted from the rock. Metal ores are generally oxides, sulfides, silicates (Table \(\PageIndex{1}\)) or "native" metals (such as native copper) that are not commonly concentrated in the Earth's crust, or "noble" metals (not usually forming compounds) such as gold (Figure \(\PageIndex{2}\)). The ores must be processed to extract the metals of interest from the waste rock and from the ore minerals.
Element | Amount | Compound | Amount |
---|---|---|---|
O | 44.8 | ||
Mg | 22.8 | SiO2 | 46 |
Si | 21.5 | MgO | 37.8 |
Fe | 5.8 | FeO | 7.5 |
Ca | 2.3 | Al2O3 | 4.2 |
Al | 2.2 | CaO | 3.2 |
Na | 0.3 | Na2O | 0.4 |
K | 0.03 | K2O | 0.04 |
Sum | 99.7 | Sum | 99.1 |
Extractive metallurgy is a branch of metallurgical engineering wherein process and methods of extraction of metals from their natural mineral deposits are studied. The field is a materials science, covering all aspects of the types of ore, washing, concentration, separation, chemical processes and extraction of pure metal and their alloying to suit various applications, sometimes for direct use as a finished product, but more often in a form that requires further working to achieve the given properties to suit the applications. The field of ferrous and non-ferrous extractive metallurgy have specialties that are generically grouped into the categories of mineral processing, hydrometallurgy, pyrometallurgy, and electrometallurgy based on the process adopted to extract the metal. Several processes are used for extraction of same metal depending on occurrence and chemical requirements.
It takes multiple steps to extract the "important" element from the ore:
- First, the ore must be separated from unwanted rocks.
- Then, the minerals need to be separated out of the ore
- Since most minerals are not pure metals, further separation methods are required.
Most minerals are chemical compounds that contain metals and other elements.
Concentration
After mining, large pieces of the ore feed are broken through crushing and/or grinding. This step creates particles that are either mostly valuable or mostly waste. TConcentrating the particles of value in a form supporting separation enables the desired metal to be removed from waste products. Froth flotation is one process for separating minerals from the surrounding worthless material by taking advantage of differences in their hydrophobicity. whereby hydrophobicity differences between valuable minerals other material are increased through the use of surfactants and wetting agents (Figure \(\PageIndex{3}\)). Flotation is used for the separation of a large range of sulfides, carbonates and oxides prior to further refinement. Phosphates and coal are also upgraded (purified) by flotation technology.
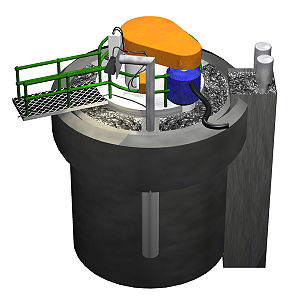
Other ways to concentration minerals include approached based on density (Froth Flotation) used if ore density is less than density of impurities, or via melting points, or magnetic properties (Magnetic separation). This can be used with magnetic ores (i.e Fe3O4) that are passed through a magnetic field, which attracts the magnetic ore and ignore the nonmagnetic impurities.
Roasting
Ore is crushed and heated to a high temp using a strong blast of hot air. The process converts the ores to their oxides which can then be reduced. Consider the natural occurring ores of zinc (\(ZnS\) (sphalerite) and \(ZnCO_3\) (smithsonite). When roasted, smithsonite decomposes to \(ZnO_{(s)}\) and \(CO_{2(g)}\) \(\ref{Roast1}\) and the hot air involved in roasting sphalerite oxidizes it \(\ref{Roast2}\) to produces \(ZnO_{(s)}\) and \(SO_{2(g)}\).
\[ZnCO_{3(s)} \overset{\Delta}{\longrightarrow} ZnO_{(s)} + CO_{2(g)} \label{Roast1}\]
\[2 ZnS_{(s)} + 3 O_{2(g)} \overset{\Delta}{\longrightarrow} 2 ZnO_{(s)} + 2 SO_{2(g)} \label{Roast2}\]
Reduction
\(C_{(s)}\) and \(CO_{(g)}\) are often used as reducing agents in simultaneous reactions. Oxides of Cr, V, and Mn are reduced using Al. During the reduction process the metal oxide is heated to a temperature above its boiling point in order to vaporize it and condense as a liquid. For example, \(ZnO_{(s)}\) that is produced in the roasting process is combined with \(C_{(s)}/CO_{(g)}\) mixture and heated at a 1100 oC. Two reduction reactions are viable at this temperature with either carbon (Equation \(\ref{Reduction1}\)) or carbon monoxide ((Equation \(\ref{Reduction2}\)) acting the reducing agent.
\[ZnO_{(s)} +C_{(s)} \overset{\Delta}{\longrightarrow} Zn_{(g)} + CO_{(g)} \label{Reduction1}\]
\[ZnO_{(s)} + CO_{(g)} \overset{\Delta}{\longrightarrow} Zn_{(g)} + CO_{2(g)} \label{Reduction2} \]
Refining
The impurities contained in the metal product of the roasting/reduction process are removed. For example, the \(Zn(l)\) produced in the reduction process often contains impurities of Cd and Pb. Though fractional distillation of Zn(l) will work in the refining process, a more commonly used and efficient method is electrolysis. The \(ZnO_{(s)}\) produced from roasting is dissolved in \(H_2SO_{4(aq)}\) and \(Zn_{(s)}\) powder is added allowing the impurities to be displaced. The solution is then electrolyzed and to get a pure metallic \(Zn_{(s)}\) as a result.
Zone Refining
A rod containing the desired pure metal and impurities is passed through a series of heating coils and cooled again. The process isolates the impurities that concentrate in the molten zones, leaving the portions behind them somewhat more pure. This process is repeated until impurities are moved to the end of the rod and cut off, resulting in an almost completely pure metal rod.
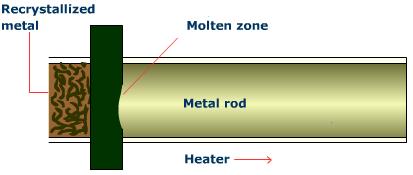
Thermodynamics of Pyrometallurgy
Pyrometallurgy is the processes of roasting an ore a high temperatures and then reducing its oxide product. Its characteristics include:
- large amount of waste as a product of concentration.
- high energy consumption to maintain high temps.
- gaseous emissions that must be controlled (i.e CO2 and SO2)
The oldest, and still the most common smelting process for oxide ores involves heating them in the presence of carbon. Originally, charcoal was used, but industrial-scale smelting uses coke, a crude form of carbon prepared by pyrolysis (heating) of coal. The basic reactions are:
\[MO + C \rightleftharpoons M + CO \label{2.1}\]
\[MO + ½ O_2 \rightleftharpoons M + ½ CO_2 \label{2.2}\]
\[MO + CO \rightleftharpoons M + CO_2 \label{2.3}\]
Each of these can be regarded as a pair of coupled reactions in which the metal M and the carbon are effectively competing for the oxygen atom. Using reaction \(\ref{2.1}\) as an example, it can be broken down into the following two parts:
\[MO \rightleftharpoons M + ½ O_2 \;\;\; ΔG^o > 0 \label{2.4}\]
\[C + ½ O_2 \rightleftharpoons CO \;\;\; ΔG^o < 0 \label{2.5}\]
At ordinary environmental temperatures, reaction \(\ref{2.4}\) is always spontaneous in the reverse direction (that is why ores form in the first place!), so ΔG° of Reaction \(\ref{2.4}\) will be positive. ΔG° for reaction \(\ref{2.5}\) is always negative, but at low temperatures it will not be sufficiently negative to drive \(\ref{2.4}\).
The smelting process depends on the different ways in which the free energies of reactions like \(\ref{2.4}\) and \(\ref{2.4}\) vary with the temperature. This temperature dependence is almost entirely dominated by the TΔS° term in the Gibbs function, and thus by the entropy change. The latter depends mainly on Δng, the change in the number of moles of gas in the reaction. Removal of oxygen from the ore is always accompanied by a large increase in the system volume so ΔS for this step is always positive and the reaction becomes more spontaneous at higher temperatures. The temperature dependences of the reactions that take up oxygen vary, however (Table \(\PageIndex{1}\)).
Reaction
|
Δng
|
d(ΔG°)/dT
|
C + ½ O2 → CO |
0.5
|
<0
|
C + O2 → CO2 |
0
|
0
|
CO + ½ O2 →CO2 |
–0.5
|
>0
|
A plot of the temperature dependences of the free energies of these reactions, superimposed on similar plots for the oxygen removal reactions \(\ref{2.4}\) is called an Ellingham diagram. For a given oxide MO to be smeltable, the temperature must be high enough that reaction \(\ref{2.4}\) falls below that of at least one of the oxygen-consuming reactions. The slopes of the lines on this diagram are determined by the sign of the entropy change.
Figure \(\PageIndex{4}\): Ellingham diagram. An ore can be reduced by carbon only if its Gibbs free energy of formation falls below that of one of the carbon reduction reactions (blue lines.) Practical refining temperatures are generally limited to about 1500°K.
Examination of the Ellingham diagram shown above illustrates why the metals known to the ancients were mainly those such as copper and lead, which can be obtained by smelting at the relatively low temperatures that were obtainable by the methods available at the time in which a charcoal fire supplied both the heat and the carbon. Thus the bronze age preceded the iron age; the latter had to await the development of technology capable of producing higher temperatures, such as the blast furnace. Smelting of aluminum oxide by carbon requires temperatures too high to be practical; commercial production of aluminum is accomplished by electrolysis of the molten ore.
In pyrometallurgy, an ore is heated with a reductant to obtain the metal. Theoretically, it should be possible to obtain virtually any metal from its ore by using coke as the reductant. For example, the reduction of calcum metral from \(CaO_{(s)}\):
\[\mathrm{CaO(s) + C(s)\xrightarrow{\Delta}Ca(l) + CO(g)} \label{23.2.1}\]
Unfortunately, many transition metals (e.g., Titanium) react with carbon to form stable binary carbides:
\[Ti + C \rightarrow TiC.\]
Consequently, more expensive reductants (such as hydrogen, aluminum, magnesium, or calcium) must be used to obtain these metals. Many metals that occur naturally as sulfides can be obtained by heating the sulfide in air, as shown for lead in the following equation:
\[\mathrm{PbS(s) + O_2(g) \xrightarrow{\Delta}Pb(l) + SO_2(g)} \label{23.2.2}\]
The reaction is driven to completion by the formation of \(SO_2\), a stable gas.
Iron Alloys of Cr, V, and Mn
- Ferrochrome ( alloy of Fe and Cr) can be produced in the reduction of Cr in an Fe compound containing its chromite ore, Fe(CrO2)2.
- Ferrovanadium ( alloy of Fe and V) can be produced in the reduction of V that occurs when adding an Fe compound to a V oxide (V2O5).
- Ferromanganese (alloy of Fe and Mn) can be produced in the reduction of Mn that occurs when adding an Fe compound to a Mn oxide (MnO2).
Titanium Production
Titanium is used in the military and aircraft industry b/c of its low density and ability to maintain its strength are high temps.
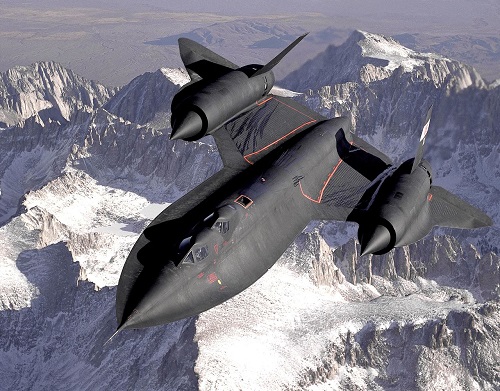
Titanium is produced using the following steps:
- Conversion or rutile or \(TiO_2\) to \(TiCl_4\) with \(C_{(s)}\) and \(Cl_2\) under high heat (> 800 oC ) \[ TiO_{2(s)} + 2C_{(s)} + 2Cl_{(2(g)} \xrightarrow{\Delta}Pb(l) TiCl_{4(g)} + 2CO_{(g)}\]
- Reduction of \(TiCl_4\) to \(Ti\) with a good reducing agent (i.e., \(Mg\) in the Kroll process) carried out at high heat (> 1000 oC ). \[ TiCl_{4(g)} + 2Mg_{(l)} \xrightarrow{\Delta} Ti_{(s)} + 2MgCl_{2(s)}\]
- Both \(Ti_{(s)}\) and \(MgCl_{2(s)}\) are electrolyzed to produces \(Cl_2\), \(Mg\) and titanium sponge (Ti enriched mass). The \(Mg\) and \(MgCL_2\) are removed via vacuum distillation (reducing of pressure with heat to preferential vaporize volatile metal that are then condenses in a separate container).
- The spong is further treated and allowed with other metal to be sold commercially.
The Kroll process is slow, expensive, and proposes a health/safety risk due to the high temperature vacuum distillation.
There are alternative means of producing titanium including the electrolysis of TiO2 pellets via the following procedure:
- The pellets are placed at the cathode end(usually Ti(s) or graphite) of an electrolytic cell.
- They are dissolved in a molten CaCl2(l) electrolyte.
- The O2- anions are discharged as O2(g) at the anode(graphite).
- The Ti4+ cation is reduced at the cathode resulting in a tatanium sponge
Copper Production
Cu ores often contain iron sulfides and to achieve a pure(uncontaminated) Cu product, the ores undergo the following processes :
Step 1: Concentration of ore by flotation (Figure \(\PageIndex{6}\).
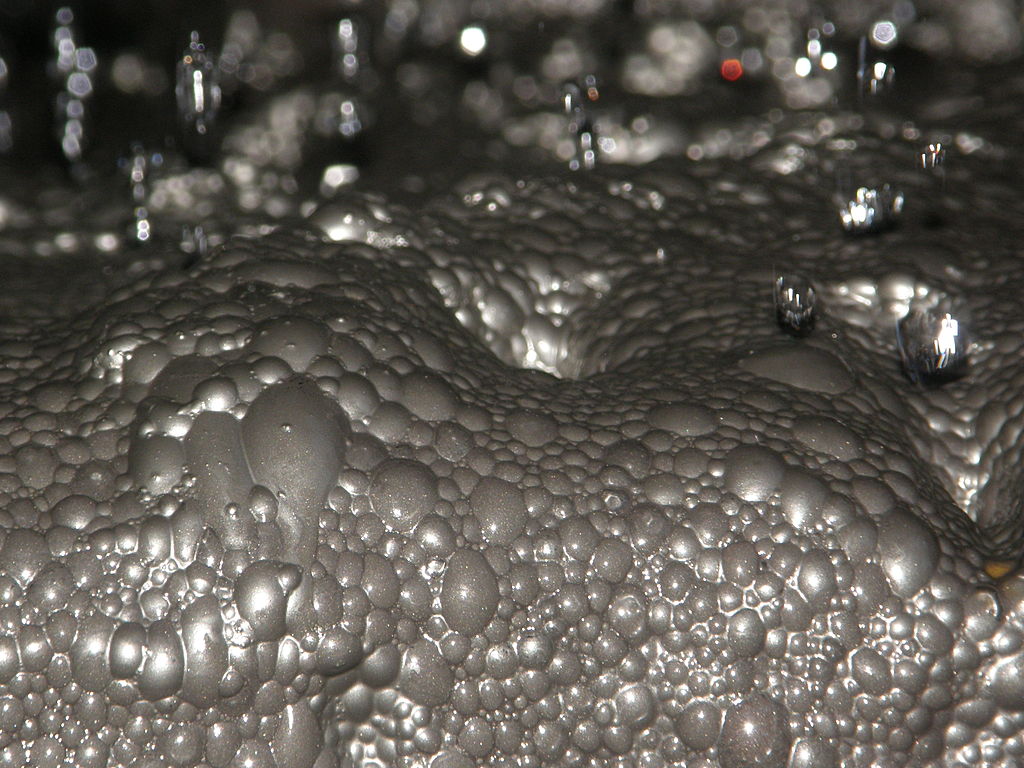
Step 2: Conversion of Fe sulfide ores to Fe oxides through roasting (e.g., roasting of Chalcopyrite ore )
\[ 2 CuFeS)2 + 3 O)2 \overset{\Delta}{\longrightarrow} 2 FeO + 2 CuS + 2 SO_2\]
Step 3: Smelting: mixing with coke/charcoal and heated at high temperatures (i.e 800 oC) for copper to keep Cu from remaining in sulfide form). Impurities are further removed by adding flux if not already present in ore (if gangue is acidic basic flux is added, if gangue is basic acidic flux (i.e., SiO2) is used. Smelting separates the material to separate into 2 layers (copper matte: bottom layer containing molten sulfides of Fe and Cu and silicate slag: top layer formed by reaction of oxides of Fe, Ca, and Al w/ SiO2).
\[FeO_{(s)} + SiO_{2(s)} \overset{\Delta}{\longrightarrow} FeSiO_{3(l)}\]
Step 4: Conversion: Air is blown through Cu matte in a separate furnace. This converts the remaining iron sulfide to iron oxide followed by the formation of FeSiO3(l) slag. The slag is poured off and the process is repeated resulting in blister copper with bubbles of SO2(g) still present.
\[2CuS_{(l)} + 3O_{2(g)} \overset{\Delta}{\longrightarrow} 2Cu_2O_{(l)} + 2SO_{2(g)}\]
\[ 2Cu_2O_{(l)} + Cu_2S_{(l)} \overset{\Delta}{\longrightarrow} 6Cu(l) +SO_{2(g)} \]
Step 5: Blister Cu is further refined through electrolysis to achieve a high-purity Cu product.
Hydrometallurgical Process
The method of refining zinc described above is an example of a hydrometallurgical process and the hydrometallurgical process eliminates the need to control gaseous emissions that are often produced in roasting. Hydrometallurgy is the process of extraction and refining that involves the use of water and aqueous solutions. It is carried out at moderate temps and is generally carried out in three steps:
- Leaching: metal ions are extracted from their ore by water/acids/bases/salt solutions. Redox reactions that occur are often essential.
- Purification and concentration: Impurities are separated either by absorption on the surface of activated charcoal, ion exchange, or water evaporation; leaving behind a more concentrated solution.
- Precipitation: the process of electrolysis is often used to precipitate the desired metal ions in an ionic solid or reduce them to their free metal.
Summary
Extractive metallurgy is the practice of removing valuable metals from an ore and refining the extracted raw metals into purer form. The field of extractive metallurgy encompasses many specialty sub-disciplines, including mineral processing, hydrometallurgy, pyrometallurgy, and electrometallurgy. Especially in hydrometallurgy, the coordination chemistry of the metals involved plays a large role in their solubility and reactivity as the ore is refined into precious metal. Many methods of extractive metallurgy may be applied to get a pure metal from its naturally occurring ore. First ores must be concentrated and separated from their earthly impurities. Concentration of ores may be achieved by froth flotation in which an ore is contained in a froth that floats at the top of a water vat. After the ore has been concentrated it must be roasted to a high temperature allowing for the desired metal to be oxidized. Once the metal is oxidized it is reduced by a reducing agent. Reduction may require the metal oxide to be heated at a high temperature. The metal must be further refined to remove all of the impurities that it may contain. Refining a metal can be accomplished by electrolysis or zone refining. Certain ores such as those of copper and titanium require special treatment before they can be refined. The extraction of iron ore is particularly important for commercial uses because of the mass production of its alloy, steel.
Problems
- Describe 2 methods of ore concentration and list the conditions under which they are used.
- Explain the conditions under which an ore might be roasted.
- Explain the conditions under which an are might be electrolyzed.
- What types of reactions occur at the cathode and anode in an electrolyzed solution?
- How might the transition metal, zinc, be refined?
- Explain the process of zone refining and how it may make an extracted metal more pure.
- Explain how a change in free energy is related to extractive metallurgy. What specific process or reaction does it pertain to?
- Give a brief explanation of why an ore might be heated to high temperatures using the principles of Thermodynamics.
- What are the characteristics of a pyrometallurgical process and how do they compare with those of a hydrometallurgical process?
- What are the applications of pig iron and how might it be refined to make pure iron.
- What are the reactions that take place in the process of making steel?
- How might an alloy of differing metals effect the properties of steel?
- Explain 2 alternative methods of extractive metallurgy and how they differ from traditional methods.
Contributors and Attributions
- Eric Knotts (UCD)
- Wikipedia
Boundless (www.boundless.com)
Binod Shrestha (University of Lorraine)
Stephen Lower, Professor Emeritus (Simon Fraser U.) Chem1 Virtual Textbook